Historia
Los primeros remaches eran pequeñas clavijas hechas de madera o hueso, y las primeras formas de metal fueron probablemente los antepasados de los remaches que conocemos hoy. Son, sin lugar a dudas, el método más antiguo conocido para unir metales, remontándose al uso más temprano de metales maleables, como los egipcios de la Edad de Bronce que remachaban las seis formas de abanico de madera en el exterior de una rueda ranurada, o los griegos que remachaban las piezas después de fundir con éxito grandes estatuas en bronce.
El remache hueco se inventó principalmente para la fabricación o el mantenimiento de arneses. No está del todo claro cuándo se inventó, pero los arneses se inventaron en el siglo IX o X. Al igual que los cascos con clavos, los arneses remachados liberaron a los esclavos del trabajo pesado, y los remaches dieron lugar a muchos inventos importantes, como las tenazas de hierro para los trabajadores del cobre y el hierro y las esquiladoras para el pastoreo de lana.
Cuando H. V. White, de la British Aircraft Company, patentó por primera vez en 1916 los remaches ciegos que se podían remachar por un solo lado, no se esperaba que se utilizaran tan ampliamente en la actualidad. Desde la industria aeroespacial hasta las máquinas de oficina, los productos electrónicos y los equipos de juegos, se puede decir que los remaches ciegos se han convertido en un método de conexión mecánica eficaz y estable.
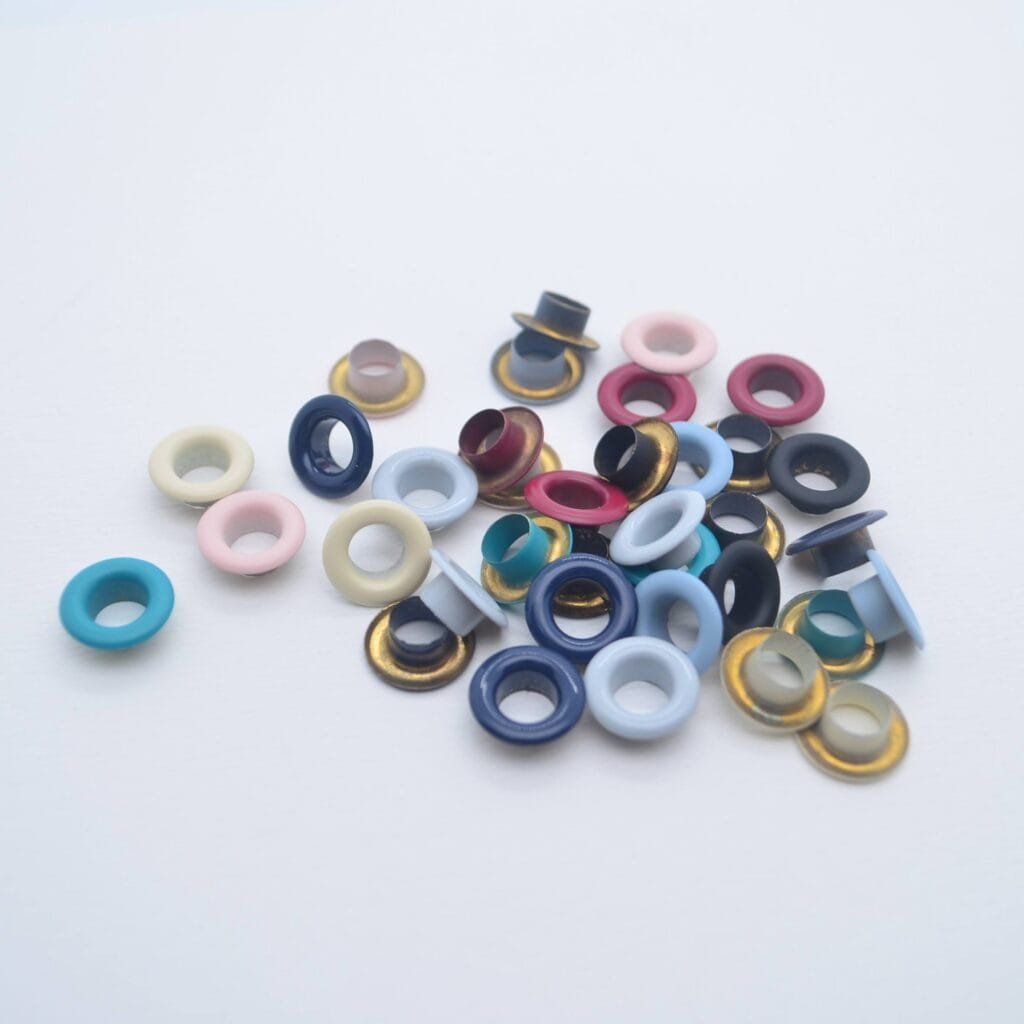
En los últimos años, el acero para embutición profunda con contenido de carbono ultrabajo se ha utilizado ampliamente en la fabricación de ingeniería mecánica y la producción de juguetes debido a sus características de alta pureza del acero, pequeño endurecimiento por trabajo en frío, buena formabilidad de embutición profunda, alta tenacidad, resistencia al desgaste y buena seguridad.
El proceso básico de fabricación de remaches huecos es el siguiente: Material del disco: decapado, fosfatado, saponificación, secado; trefilado en frío; recocido de recristalización; trefilado fino; moldeo por extrusión en una máquina de estampación en frío de varias estaciones (incluido el corte, el recalcado y el ahuecado); niquelado o galvanizado de la superficie; prueba de “rayado”; embalaje y almacenamiento. En la prueba de “abocardado” (es decir, la prueba que simula la condición de remachado de un remache hueco), la parte hueca del remache se comprime para producir expansión y rebordeado. El proceso de rebordeado es similar al proceso de moldeo por escariado y rebordeado de una placa delgada. El borde exterior de la parte hueca tiene la mayor fuerza y deformación, por lo que el rendimiento de moldeo del material es muy alto. Al rebordear, a veces se producen grietas, rebordeado y otros defectos.
(1) Hay cinco tipos de defectos en la conformación por estampación en frío de remaches de acero con contenido de carbono ultrabajo: grietas por recalcado, grietas por rebordeado, recalcado hacia abajo, grietas por deslizamiento y rebordeado incompleto.
(2) El proceso de producción debe controlar principalmente la baja temperatura de calentamiento de la palanquilla (1150 ~ 1 200 ℃) y controlar estrictamente la temperatura de hilado del alambre de la varilla de alambre a 910 ~ 930 ℃, de modo que la varilla de alambre terminada tenga un tamaño de grano moderado, el grado 6 ~ 6.5 es apropiado; Mejorar la calidad de la superficie de la varilla de alambre.
(3) En términos del uso de materiales, el rendimiento de conformado por estampación en frío de los materiales debe mejorarse ajustando la deformación por estirado y adoptando el proceso de recocido correspondiente en el proceso apropiado, a fin de reducir o eliminar los defectos de conformado por estampación en frío, tales como agrietamiento de rebordeado, recalcado hacia abajo y rebordeado incompleto.
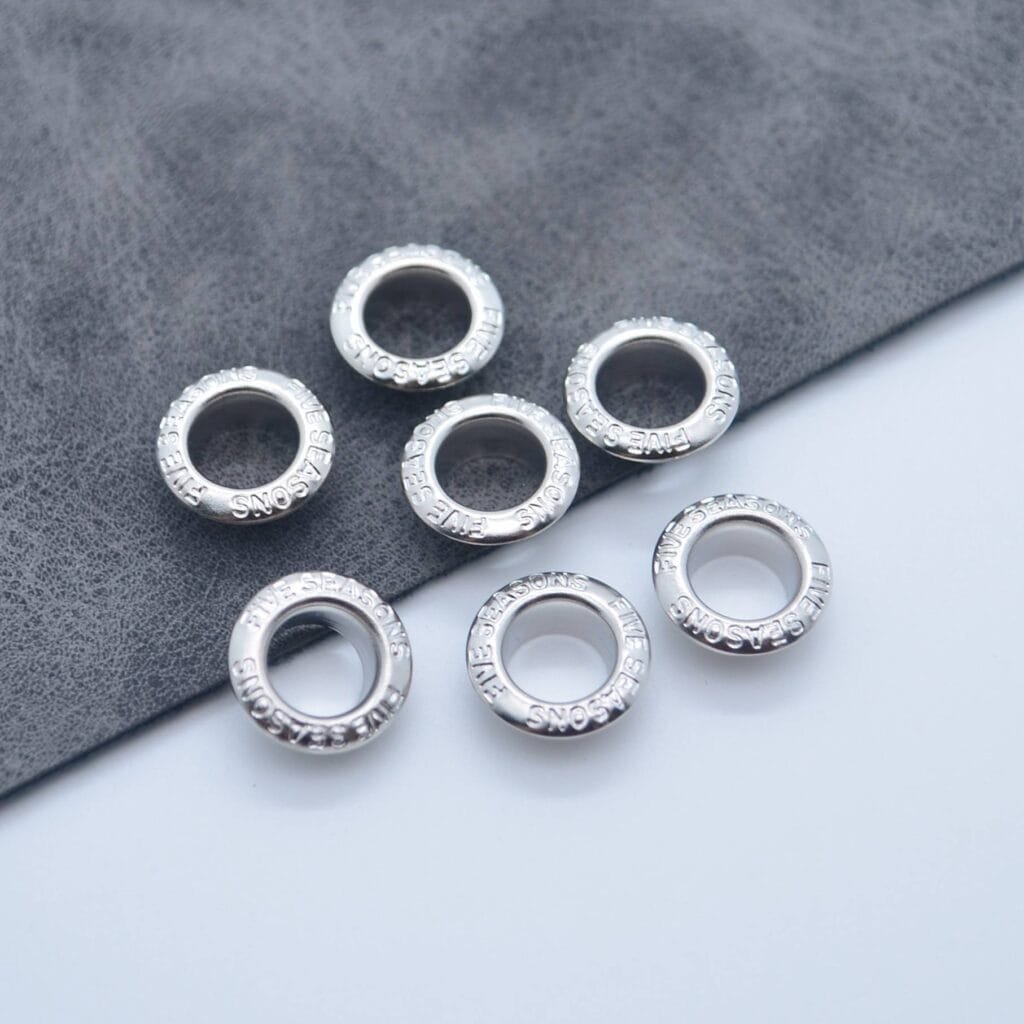